Introduction
Today I am displaying an 11th-century Russian-style quiver for crossbow bolts. The piece was constructed using woodworking, leather carving, leather dying, and bronze-smithing. I built this item after purchasing a crossbow in September 2020 and needing a way to carry my bolts (which were also made by me). Overall this project took approximately 40-50 hours to complete, over September-December 2020. This was my first significant leather and woodworking project for the SCA. I learned a lot in the process, and am quite happy with the final result.
Historical Context
Crossbows were widely introduced to the Rus’ territories most likely by the 11th century. There is mention that a type of early crossbow was used for hunting as early as the 10th century. Although crossbows themselves have not been found in the archeological record, bolts and bolt heads have been discovered in Novgorod dating as early as the 1170s. The Russian Chronicles from 1184 mention crossbows being used in battle with the Polovtsians. By the 13th-14th centuries, crossbows were widely in use by soldiers, especially in the defense of cities from siege. A few remaining crossbows from late period or just post period are stored in the Moscow Armory Museum, and show that they were quite similar to those in use in Western Europe. [Medvedev, “Crossbows.”]
I decided to purchase and start using a crossbow for mundane reasons (shoulder injury) which prevented me from firing a regular bow. My persona is from the mid-11th century, which would have been early on in the use of crossbows in Rus’, although it is possible they may have been in seen given the widespread trade from Northern Europe and the Middle East which traveled through Rus’ and Volga Bulgaria in that time.[Valeev, “Trade Relations…”] As I started creating bolts for my crossbow, I also started researching medieval crossbow quivers, but was unable to find any details about crossbow quivers prior to the 16th century or so in Russia. All existing remnants are from much later in period or post-period. A few earlier manuscripts depict Rus’ soldiers with crossbows, but none that I could find depict quivers on those crossbowmen. As a result, I posited that Rus’ crossbowmen would have used quivers similar to those used by bow archers.
Illumination from the Radziwiłł Chronicle, showing Rus’ crossbowmen in action. Image from Medvedev, A.F. “Kolchan i Naluch’e.” Ruchnoe metatel’noe oruzhie (luk i strely, samostrel): VIII-XIV vv. Moscow, 1966, illus. 1. Image depicting a Rus’ warrior hunting an eagle while carrying a hip quiver, from the cladding over an aurochs horn. Image from Rybakov, B.A. “Drevnosti Chernigova.” Materialy i issledovanija po arkheologii SSSR. 1949 (11), illus. 20.
As quivers were made of perishable materials (wood, birch bark, leather, bone), little has been found in archeological finds from period Rus’ quivers. Many graves of archers still have piles of arrowheads and metal components indicating a quiver was likely once present, but with few or no surviving elements from the quiver itself. A few surviving examples, such as one found in the ruins of the Church of the Tithes, where a large number of Kievans were trapped and interred when the church was set alight and destroyed by the Mongols in 1240, indicate that in the pre-Mongol Invasion Rus’ period (9th-13th century), there were two main types of quivers in use in Rus. The first type was made from a cylinder of birch bark, sewn along the back, with a wooden bottom and a bone flap sewn into the seam, used to hang the quiver from the belt. The second (or “semi-cylindrical”) type had a back and bottom connected in an “L” shape, with a front made of leather. Some examples have been found with metallic rings or plates that were used to decorate the leather, but these were not universally present. These quivers typically were wider at the bottom than at the throat, and made use of two metal brackets attached to the side of the backboard; a strap running from the belt, through one bracket, across the face of the quiver, through the second bracket, and back to the belt was used to suspend the quiver. Medvedev’s book includes images of about a dozen of these brackets found in various graves. [Medvedev, “Quivers and Bowcases”] Note that Medvedev’s drawing shows a strap with a hook attached to the bottom of the quiver. Medvedev explains that this was an optional feature, used by horseback archers to help steady the quiver when riding. As I do not participate in equestrian activities, I decided to omit this strap.
Rus’ quiver, possible reconstruction. Image from Medvedev, A.F. “Kolchan i Naluch’e.” Ruchnoe metatel’noe oruzhie (luk i strely, samostrel): VIII-XIV vv. Moscow, 1966, plate 1. The first two images are the semi-cylindrical type. The third shows a birch-bark cylindrical quiver. Metal findings from Rus’ quivers. Image from Medvedev, A.F. “Kolchan i Naluch’e.” Ruchnoe metatel’noe oruzhie (luk i strely, samostrel): VIII-XIV vv. Moscow, 1966, plate 7.
As I was unable to find a source for birch bark in large enough sections to work for a quiver, I decided to model my quiver from the second, semi-cylindrical type. Medvedev states that these were in common use amongst professional soldiers (druzhinniki) from the 9th-11th centuries, a convenient time-frame for my persona.
To decorate the leather, I decided to do leather carving with a design that would have been meaningful for my persona. The existence of dvoeverie or “dual-faith” was strongly pronounced in Russia from the acceptance of Christianity as the official state religion in 988 right on through the entire medieval period, but it was especially pronounced during my persona’s period, circa 1050. The simargl, a fantastic dog-headed bird, was possibly adapted from the image of the senmurv in Persia via trade relations with the Caucasus or Volga Bulgaria. This image was strongly associated with the holiday of Rusalia and St. John’s Day, that is, holidays associated with the solstice. The simargl was seen as a protector of crops and vegetation, as well as a protector of sailors on Rus’s riverine highways. As my persona is a sailor and trader sailing those rivers, I decided to adopt that image for my quiver. The image for the quiver came from a mold that was used for casting silver bracelets with an image of two simargls entwined in knotwork. This knotwork form of imagery was particularly popular starting in the 11th century through the Mongol invasion in 1240. [Rybakov, “Rusalias…”]
Leather crafting has been well-documented in the archeological record for medieval Rus’. In particular, significant numbers of finds have been documented from Novgorod, where they were well preserved in layers that have been precisely dated using dendrochronology (that is, based on tree rings for the many layers of wood that were used as roads in the city). S.A. Izyumova published an article which goes over these finds in great depth. Based on finds, it seems that many of the same processes used for leather today (tanning, dyeing, carving, stamping, stitching) are quite similar to those used today, with the except of the specific chemicals used in modern day. Tanning was done using tree-based tannins, much like modern vegetable-based tanning processes. Dyes existed to turn leather various colors, as documented by mention in the Chronicles from the time (eg., Prince Yaroslav Vladimirovich was known for his green leather shoes, and red leather shoes/boots are commonly seen on royalty and boyars in various icons and illuminations). Although the vast majority of leather-related finds in Novgorod have been shoes or shoe-parts, some other types of items have been discovered, including stamped leather intended for quivers. [Izyumova, “Leatherworking…”]
The number of findings for quivers discovered in Rus’ are extremely small in number. All finds to date have been made of iron, which is somewhat surprising given that non-ferrous metals (brass, bronze) were widely used in jewelry and other decorative arts in Rus’ throughout period, and would have been less susceptible to rust damage. I suspect that the few finds to date are quite possibly non-indicative and that, especially for members of the upper class or nobility, findings may have been created instead from bronze or brass to imitate the look of gold. Forging findings from iron was beyond the scope of this project as I don’t have ready access to a forge hot enough to work that material. I instead decided to use bronze, which was more readily workable with my existing tools and skills.
Materials
- 6-7 oz Oak Vegetable Tanned Leather
- 3.5-4 oz Oak Vegetable Tanned Leather
- Birch Wood, 1/2″ thick
- Brass Nails
- Bronze Wire, 4 ga
- Fiebings Pro Leather Dyes (Tan, Green, Turquoise, Red, Yellow)
- Titebond Genuine Hide Glue
- Waxed Hemp Thread
All of these materials are reasonably period, with the exception of the alcohol-based dyes. Period dyeing techniques existed[Charlotte, “Medieval Leather Dying”; Izyumova, “Leatherworking…”], but would have required creating dyes from scratch; I decided instead to focus on the leathercarving/stamping, and to use modern dyes due to availability.
I used birch wood as it would have been readily available in Rus’, where the birch tree (Rus. beryozka) had significant sociological and magical significance. The birch tree was strongly associated with the same holidays as the simargl design, and was commonly used to produce wooden crafts. [Rybakov, “Rusalias…”]
The use of hide-based glue is well-documented in period.[see for example, Theophilus, On divers arts, p. 16]
As this item was intended for use outdoors and in potentially wet/humid environments, I used some modern materials to coat the wood and leather to help make them more waterproof.
- Fiebings Resolene Finish (acrylic-based finish to seal and protect leather)
- Minwax Water-Based Polycrylic Spray (acrylic-based finish to seal and protect wood)
- Seiwa Tokonole Leather Finish (composed of natural waxes, used to seal the raw edges and back of the leather)
Methods and Construction
The first step in creating this quiver was to come up with a design. As I was unable to find any pre-Mongol Rus’ examples of quivers for crossbows, I started with the semi-cylindrical design described in Medvedev’s work. She shows one possible example of how such a quiver could have been designed, but I took some liberty with extending the leather over the sides of the “throat” for decorative reasons. My first draft was significantly more flared at the ends and constricted in the middle, but after creating a model out of poster board, I found this was too narrow to easily carry a dozen bolts. My second draft worked much better in poster board trials and more easily allowed me to store or retrieve bolts. As such, I decided to go with this pattern. It is still moderately flared at the bottom, with a 5″ base which constricts to 4″ about 40% of the way up, and then stays at that width for the remaining length. Medvedev states that standard quivers were 60-90 cm long (23-35 inches) for standard sized arrows. My bolts are 18″ long, so I adjusted the length accordingly. The base is still about 5″ in diameter, as was common for semi-cylindrical full-sized quivers. Since I’m still storing the same number of bolts as quivers, the widths would still need to be relatively similar. The full-sized quivers tended to flare again at the top since arrows were stored fletches up. I assumed that, as was common in Western Europe, crossbow bolts would be stored fletches down, so no additional flare was needed at the top. Storing the fletches down would allow the bowman to select from bolts with different points intended for different purposes, such as birds vs. small game vs. large game, or leather/chain armor vs. plate.
I ordered the wood for the back and bottom, using Russian birch. As hoped, I was able to find it in 1/2″ thickness. This gave me an idea how much overlap I needed at the side and bottom for the leather, as well as how wide my brackets could be. The wood ended up taking nearly a month to arrive, but once it finally did, I drew out the shapes on the board, rough cut to size, and then used a belt sander to grind them down to the correct shape. I used hide glue and brass nails to attach the wood pieces. After driving the first two nails, I noticed the wood started to crack on the backboard. The cracks were not too large as to cause a structural issue (yet), so I filled them with a mixture of glue and sawdust, and pre-drilled holes for all nails thereafter to make it easier for them to penetrate the wood without causing too much expansion. This worked well and I didn’t see any further cracking. The wood was stained brown, and I glued a semicircle of thin leather to the bottom to help prevent the bolts from damaging or bouncing against the bottom. I then sprayed the interior with polycrylic to protect the wood from water and damage. I took care of this side at this point, since it would be difficult to do later once the leather was attached.
While I was waiting for the wood to arrive, I started working on the leather. Cutting out the pattern piece was relatively easy, then I transferred the design to the leather using a sheet of acetate and a stylus. The original design had some “questionable” knotwork (e.g. lines that lead nowhere) but I left it as is, as it’s pretty common, especially for Viking and Rus’ knotwork, to not fully make sense. I carved the design with an Xacto knife (didn’t have a swivel knife available at the time, unfortunately), and then started stamping along all the edges. The areas around the head and the inner spaces between the knotwork were also stamped with a background tool to help distinguish the pattern. The areas of the pattern were “painted” with dye and a paintbrush to fill in the red, yellow, green and blue areas. Carving the pattern first helped prevent the dye from soaking from one area of the pattern to another, and I found this to be easier than I had dreaded. The background areas inside and immediately next to the design were also dyed brown using a brush, and then I used a wool dauber to dye the remaining background. All areas required 2-3 layers of dye to get all of the colors to be consistently uniform. I rubbed some Fiebings leather Antique Finish (basically dye in a paste form, very similar to shoe polish) and buffed it off to stain the cut edges and help make the design “pop.”
To help preserve the leather and waterproof it, I used Seiwa’s Tokonole product to seal the raw edges and back surface. This product is made of waxes, but looks and feels similar to white glue. To seal the leather, I applied a layer of the Tokonole, then rubbed the surface with a smooth-edged glass burnisher. This “glues” the surface together to make it less rough and more resistant to water. To protect the opening, I cut out a strip of lightweight leather, and used it as “bias tape,” running it around the opening. The tape was glued down with hide glue (binder clips worked great for holding it in place while the glue dried), then I punched holes and stitched along the tape.
To assemble the quiver, I predrilled holes through the leather and into the wood every half-inch. Because the leather flares in the bottom half, lining up the leather over the board while flat was difficult, but when I curled the leather into shape, it lined up perfectly, since the board width matches the leather’s semi-circular diameter. Once the holes were drilled, I applied glue to the board edge and started driving brass nails through the leather into the board to hold it fast. This approach worked great, and held the leather fast to the wood. Once the first side had been attached and dried, I drilled holes along the second side, and glued/nailed down the leather on that side. I discovered there was a small gap between the leather and the bottom edge, so I glued in a small strip of thin leather to fill the gap, then drilled, glued and nailed along the bottom edge.
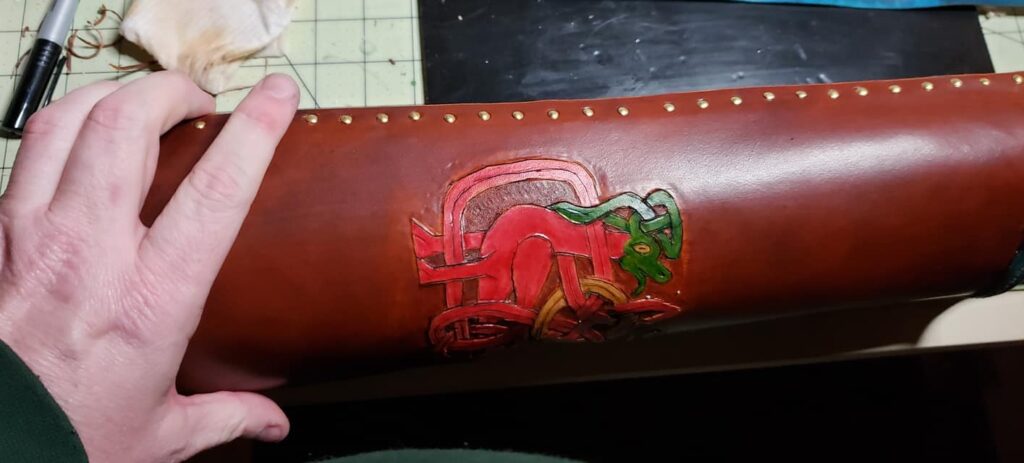
At this point, all that was left was to create the brackets and attach them to the side. The images in Medvedev’s book (see above) showed them attached by rivets, which would make sense if they were attached to the leather rather than the wood. But, the reconstruction shows the brackets being inserted directly into the backboard, which would not require a rivet and could be done with a simple nail. I decided to use nails, as having the brackets align with the backboard would be better for suspending the quiver from the belt, as the further forward the brackets were located, the more likely the quiver top would be to lean outward. I knew that my brackets could be up to 1/2″ wide to fit over the width of the board. The brackets were created using 4 ga bronze wire. The two sides were forged out into leaf shapes, then the center was bent around a mandrel to create the central arch. The leaf central “vein” was created using a file, and then each leaf was punched with two holes for attachment. I then drilled corresponding holes on the quiver and attached the brackets using brass nails.
Bronze brackets Brackets attached
Once the work had been assembled, I polyurethaned the back and bottom, and coated the front with Resolene to seal the dye and waterproof the leather.
The final step was to dye and cut a leather strap to hang the quiver from a belt. By passing this across the front and through the brackets, it was easy then to run the straps to the belt and adjust to the appropriate length. I then punched holes and sewed the belt loops to length. The leather strap was stamped with a serpentine pattern, but because the leather was so thin, the pattern isn’t as visible as I had hoped. I ended up replacing the strap with a thicker one that took the pattern better, and should be more sturdy.
The final product:
Testing the length Final product
Lessons Learned
The brown dye I used for the background leather turned out much darker than expected, especially after applying three layers to even out the tone. I later read online that for lighter colors, it is possible to cut the dye so that it applies in lighter, thinner layers and doesn’t get as dark as a result. I might try this on a future project to see if I can lighten up the color.
The birch wood turned out to be much harder than expected. It was quite difficult to cut with my available tools (handsaw, jig saw), and became even more problematic when attempting to drive nails. The nails had a tendency to cause the wood to split and crack. After seeing this with the first two nails I drove to attach the bottom to the back, I started pre-drilling pilot holes for all subsequent nails. Even this was difficult, as I had two drill bits snap inside the wood, and are still there! I subsequently used carbide drill bits, which seemed to have better luck handling the dense wood, but the process still remained quite time consuming.
Many thanks to THL Roibeard mac Neill mhic Ghille Eoin (mka Louis Garcia) for his advice and teaching on the bronzesmithing technique used to create the brackets from bronze wire.
Bibliography
- Charlotte, Ron (in SCA, known as Al Thaalibi). “Medieval Leather Dying.” 1996. Downloaded September 2020 from http://www.personal.utulsa.edu/~marc-carlson/leather/ld.html
- Theophilus. On divers arts. New York: Dover Press, 1979. ISBN 0-486-23784-2.
- Валеев, Р.М. «Торговля Волжской Булгарии с Северной и Западной Европой в Домонгольский Период (IX – начало XIII века).» Вестник НГУ. Серия: История, филология. 2011 (3). с. 175-182. / Valeev, R.M. “Torgovlja Volzhskoj Bulgarii s Severnoj i Zapadnoj Evropoj v Domongol’skij Period (IX – nachalo XIII veka).” Vestnik NGU. Serija: Istorija, filologija. 2011 (3). pp 175-182. [“Trade Relations of Volga Bulgaria with Western Europe in the Pre-Mongol Period (9th-early 13th centuries).” NSU Bulletin. Series: History, Philology.] Translation to English available on my blog at https://rezansky.com/trade-relations-between-volga-bulgaria-and-northern-and-eastern-europe-in-the-pre-mongol-period-9th-early-13th-cent/
- Изюмова, С.А. «К истории кожвенного и сапожного ремесел Новгорода Великого.» Материалы и исследования по археологии СССР. 1959 (65), с. 192-222. / Izjumova, S.A. “K istorii kozhevennogo i sapozhnogo remesel Novgoroda Velikogo.” Materialy i issledovanija po arkheologii SSSR. 1959 (65), pp. 192-222. [“Toward a History of the Leather and Shoe-working Arts in Novgorod the Great.” Materials and Research on the Study of Archeology of the USSR.] Translation to English available on my blog at https://rezansky.com/leatherworking-and-shoemaking-in-novgorod-the-great/.
- Медведев, А.Ф. «Колчан и Налучье.» Ручное метательное оружие (лук и стрелы, самострел): VIII-XIV вв. Москва, 1966, с. 19-25. / Medvedev, A.F. “Kolchan i Naluch’e.” Ruchnoe metatel’noe oruzhie (luk i strely, samostrel): VIII-XIV vv. Moscow, 1966, pp. 19-25. [“Quivers and Bow-cases.” Manually Thrown Weapons (Bow and Arrows, Crossbows), 8th-14th centuries.] Translation to English available on my blog at https://rezansky.com/quivers-and-bow-cases-in-medieval-rus/.
- Медведев, А.Ф. «Самострел.» Ручное метательное оружие (лук и стрелы, самострел): VIII-XIV вв. Москва, 1966, с. 90-96. / Medvedev, A.F. “Samostrel.” Ruchnoe metatel’noe oruzhie (luk i strely, samostrel): VIII-XIV vv. Moscow, 1966, pp. 90-96. [“Crossbow.” Manually Thrown Weapons (Bow and Arrows, Crossbows), 8th-14th centuries.] Translation to English available on my blog at https://rezansky.com/crossbows-in-medieval-rus/.
- Рыбаков, Б.А. «Древности Чернигова.» Материалы и исследования по археологии СССР. 1949 (11). с. 7-102. / Rybakov, B.A. “Drevnosti Chernigova.” Materialy i issledovanija po arkheologii SSSR. 1949 (11), pp. 7-102. [“Antiquities of Chernigov.” Materials and Research on Archeology of the USSR.]
- Рыбаков, Б.А. «Русалии и Бог Семаргл-Переплут.» Советская археология, 1967 (2), с. 91-116. / Rybakov, B.A. “Rusalii i Bog Semargl-Pereplut.” Sovietskaja arkheologija, 1967 (2), pp. 91-116. [“Rusalias and the God Semargl-Pereplut.” Soviet Archeology.] Translation to English available on my blog at https://rezansky.com/pagan-elements-in-the-decorative-art-of-medieval-rus-rusalia-simargl-and-pereplut/.